Production Process
PRODUCTION FACILITY
At Ariane, we take pride in our 200,000-square-meter production facility, which houses state-of-the-art machinery capable of producing up to 15 million pieces of the hotel and retail dinnerware annually. Our commitment to using the latest technologies, such as Isostatic presses and fast-firing roller kilns, combined with raw materials of the highest quality sourced exclusively from Europe, enables us to craft the world’s finest porcelain dinnerware.
Our porcelain manufacturing process involves production, processing, and finishing. However, what sets us apart is our precise methodology, passion, and sound technical know-how that goes into every product. Our team of 750 highly skilled employees brings their expertise, attention to detail, and vast experience to ensure that each and every Ariane Porcelain product surpasses the highest standards of the HORECA industry.
We believe that crafting something truly extraordinary requires an unwavering commitment to quality and excellence. That’s why we are dedicated to producing the finest porcelain dinnerware in the world, designed and built to perfection. With our products marketed and shipped to over 55 countries worldwide, we are proud to be at the forefront of the dinnerware industry.
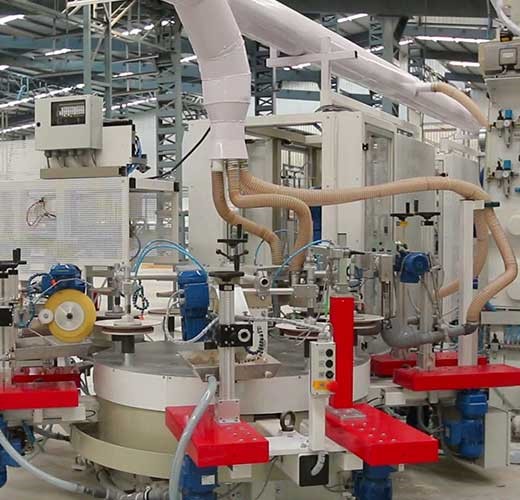
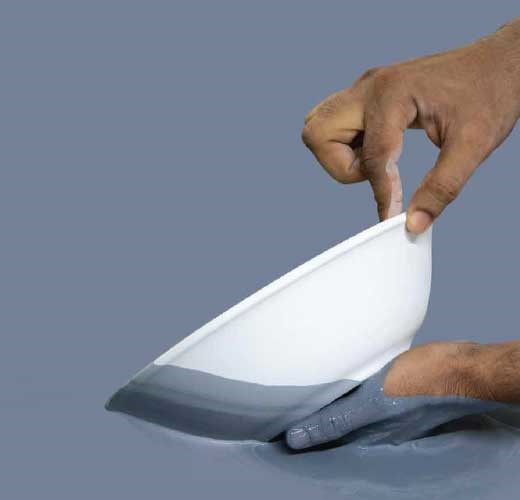
BODY & GLAZE PREPARATION
As a manufacturer, we are proud to produce high-quality ceramics with unique body and glaze recipes. Our team of skilled experts has formulated a proprietary blend consisting of four essential components: feldspar, quartz, kaolin, and free alumina. Each ingredient is milled to a specific consistency and carefully combined to create the perfect recipe for our ceramics. This secret formula is a testament to our commitment to excellence.
Once our unique blend is prepared, we subject it to a magnetic process to eliminate any free iron particles that may be present. These iron particles are collected for use in other applications. The resulting mixture is then utilized in various forms depending on the intended purpose. It is transformed into dry granules for Iso pressing, shaped into wet clay rolls for creating cups and mugs with a wheel-turning method or converted into a liquid slurry for high-pressure and manual casting.